Aside from water, concrete is the most-used material in the world, with about 14 billion cubic meters being used every year. Of that, 40% of that is used to build places for people to live.
If you were to pour that amount of concrete to make a paving slab ten centimeters thick, it would cover all of England and about half of Wales. In the US, the same amount would cover the state of New York.
But concrete production releases carbon dioxide (CO₂), one of the greenhouse gases that drives climate change.
About 90% of emissions associated with concrete come from the production of Portland cement — this fine grey powder, the part that binds concrete ingredients together, was named after its resemblance to stone from the Isle of Portland, Dorset.
Portland cement accounts for 7%-8% of the world’s direct CO₂ emissions.
Production of a more sustainable and cost-effective low-carbon cement, often nicknamed “green” cement, is scaling up. A new plant next to an existing cement plant in Redding, California, will produce about 15,000 tons of low-carbon cement every year.
This could be used to make about 50,000 cubic meters of concrete, which is less than 0.0004% of the world’s concrete production.
At Redding, materials technology company Fortera turns CO₂ captured during conventional cement production into ready-to-use green cement, a form of calcium carbonate. This could reduce carbon emissions of cement by 70% on a ton-for-ton basis, according to Fortera.
A concrete issue
People have been using concrete for more than 2,000 years, by blending gravel, sand, cement, water and, sometimes, synthetic chemicals. It’s used to create everything from paths and bridges to buildings and pipes.
Currently, the EU uses more than two tons of concrete per person per year — 325kg of that is cement. That’s equivalent to the amount of food the average European person eats in five months.
Cement production is an energy-intensive process and the greenhouse gas emissions are hard to cut. When limestone is heated in a kiln, often fueled by coal, nearly half that limestone is lost as CO₂ emissions.
This happens because limestone (calcium carbonate) breaks down in heat to form clinker, a mix of calcium oxide and CO₂. For every ton of ordinary Portland cement made, 0.6-0.9 tons of CO₂ are released into the atmosphere.
So many industries rely on this material. The main challenge facing the cement industry is reducing CO₂ emissions at the same time as meeting global demand.
So as well as developing new technologies, low-carbon cement production must be established on a global scale to meet infrastructural needs required of economically developing nations.
Low-carbon alternatives
Other ways to reduce the carbon footprint of concrete include using fly ash (a by-product from burning coal in power plants) or slag (a by-product from steel production) to partially replace Portland cement.
However, sources of these materials will reduce as other industries decarbonize. Over time, less iron ore will be used to produce steel as more steel is produced from recycling existing steel, so there’ll be less available slag.
Current strategies for decarbonizing cement and concrete rely heavily on using carbon capture and storage technology to capture unavoidable process emissions from cement plants.
So low-carbon cement production doesn’t have to involve replacing every cement production plant in operation. Low-carbon cement facilities can be retrofitted to capture CO₂ emissions released from manufacturing conventional cement.
Plants can also use that captured CO₂ within the cement that they are producing or as a product for the food and chemical industries.
In Norway, Heidelberg Materials are building an industrial-scale carbon capture and storage plant at a cement facility that could capture and store an estimated 400,000 tons of CO₂ per year — that’s half the existing plant’s emissions.
However, this technology has a high investment cost for cement producers. Captured CO₂ can be stored underground, but this requires specific geological characteristics that aren’t guaranteed at cement production sites.
Greenhouse gas emissions in the cement sector are regulated by the EU’s emissions trading system. This was established to make polluters pay for their greenhouse gas emissions, reduce emissions and generate revenues to finance the green transition.
This legislation has not significantly reduced carbon emissions in the cement sector over the past decade, according to the International Energy Agency, mainly due to free emissions allowances being granted to cement manufacturers.
Despite sustained healthy profits in the cement industry, there hasn’t been enough investment in the widespread uptake of cleaner technologies and the sustainable use of materials.
Greater financial incentives could help whereby companies have to pay for emissions associated with the production of cement.
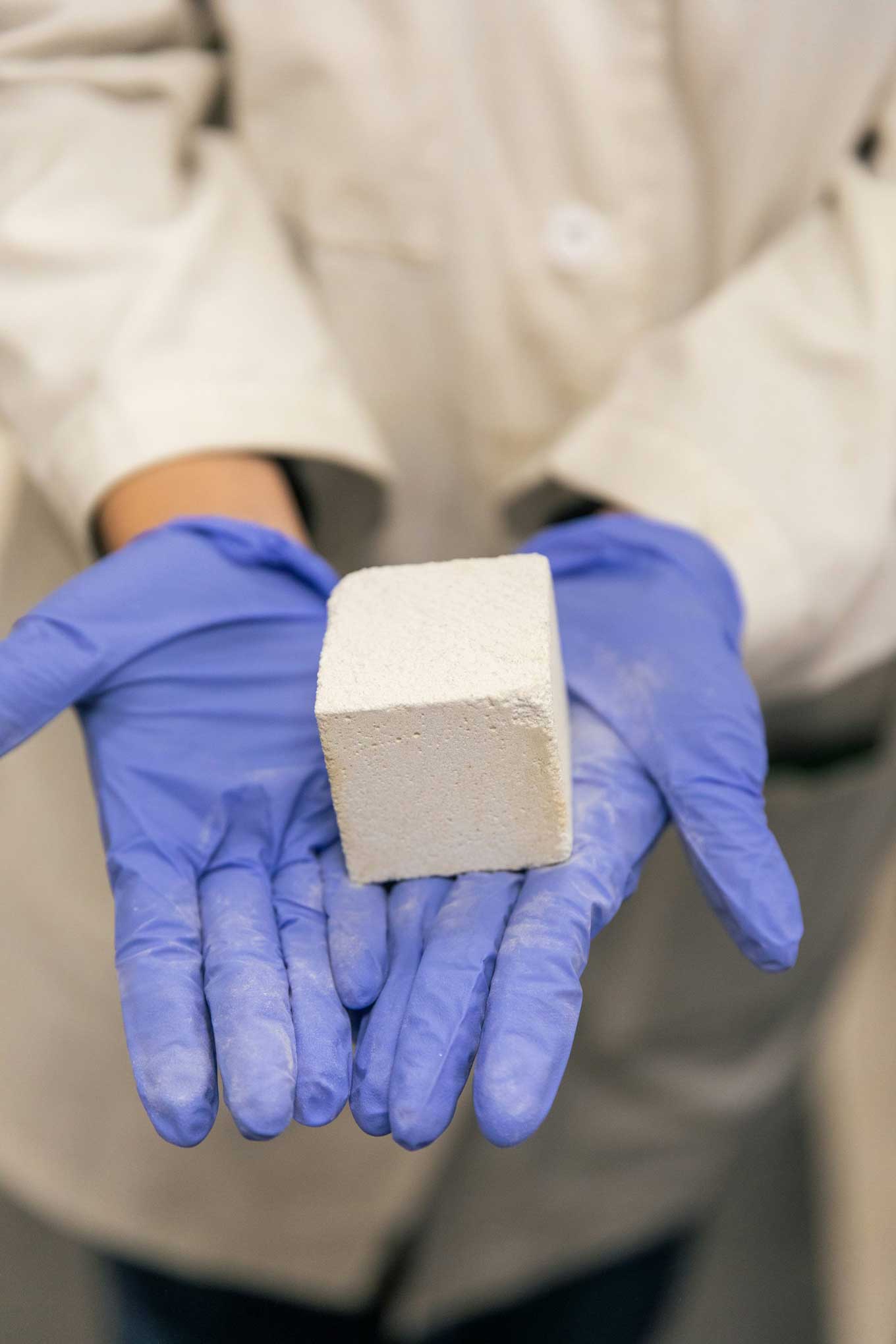
As a design engineer, I appreciate that material choice and good design play a major role in the sustainability credentials of construction.
Before low-carbon cement technology becomes more widespread, engineers, designers and builders can use construction materials more efficiently and choose products with lower embodied carbon — that’s carbon emissions released during the life cycle of building materials, from extraction through to disposal.
This approach could easily save 20% in embodied emissions associated with new building design.
Some governments could move towards only permitting the use of low-carbon cement. In Ireland, the Climate Action Plan 2024 requires that low-carbon construction methods and low-carbon cement are specified where possible for government-procured or government-supported construction projects.
Could all cement in the future be low-carbon or “green”? How “low-carbon” is defined will play a very important part in how this is translated into practice in the industry.
Retrofitting technology to large-scale existing cement production plants will prove that it’s technically possible to produce low-carbon cement efficiently at scale.
With the right incentives in place by governments and the construction sector, almost all cement produced around the world could be low-carbon.
This article by Jamie Goggins, from the University of Galway, was originally published by The Conversation.